Rocket Lab (RKLB) - Deep Dive #2
The first private company ever to put a satellite in space was SpaceX; The second was Rocket Lab.
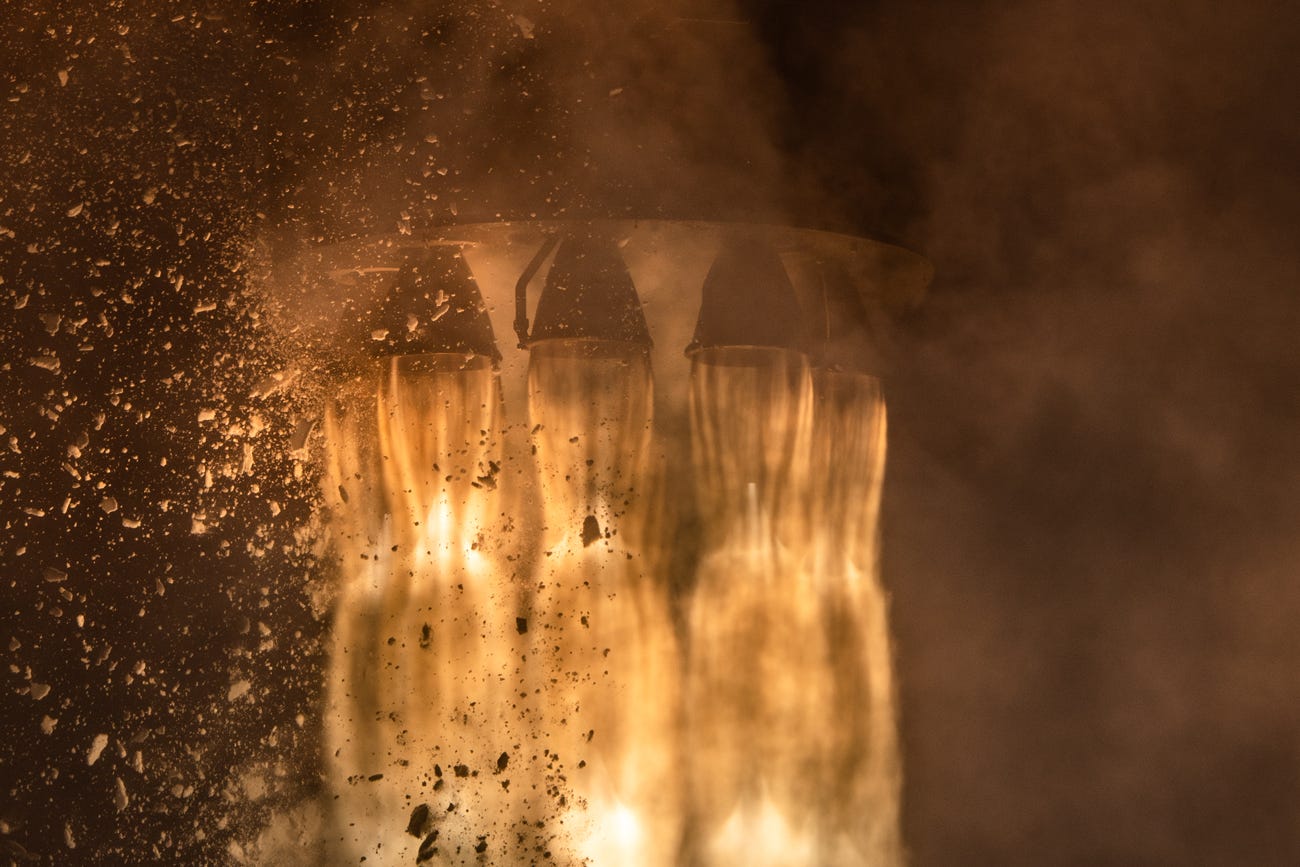
Disclosure: This is not financial advice. If you like the idea, conduct extensive research and consult a financial advisor before making any investment decisions. All investments, including this one, carry the risk of financial loss. I own Rocket Lab stock, thus I am biased in favor of the company and one should view this article through that lens. This article comprises my personal beliefs and convictions around owning any securities mentioned, and is not intended to be used as a recommendation to buy or sell any securities. Please be careful everyone.
*as a thank-you to the Rocket Lab community, this article and all RKLB updates will remain free for all subscribers in perpetuity
Introduction
Rocket Lab is an end-to-end space company specializing in building, launching, and maintaining satellites on orbit. They have deep connections with numerous government organizations and a growing network of private customers. Rocket Lab offers these customers access to space and the tools to build things for space, and I believe demand for their services will grow exponentially as low Earth orbit (LEO) becomes the next hottest destination. Featuring an extremely impressive list of accomplishments given they started from nothing, 10% CEO/Founder ownership, and a stacked executive team and BOD including numerous ex-Lockheed, ex-Boeing, ex-government regulators, Rocket Lab is shooting for the stars and I think they’ll make it.
This article is meant to serve as a deep-dive into Rocket Lab’s past, present, and future. I feel that Rocket Lab’s unique history and humble beginnings are extremely important to the investment thesis as they showcase just how far the company has come with so little startup capital - reaching new heights every year, faster, cheaper, and more reliably than any rocket program in history.
Rocket Lab is a company I have been following for years. Being a space nerd, I’d heard their name tossed around often and I knew they were trying to corner small launch - what I didn’t anticipate was how successful they would be at that. I only started paying real attention to the company around 2021, when it was made clear that Rocket Lab was developing the Neutron rocket to compete directly with SpaceX’s Falcon 9 in medium launch. At the time, I thought they were fools for this.
But after re-examining the company a few years later, I believe Rocket Lab not only has immense potential to compete with SpaceX and others, but that it could outcompete the industry by a wide margin, in launch and everything else.
Table of Contents
Introduction
Thesis & PTs
Risk Factors
Notable Missions & Contracts
Business & Financials
Launch
Electron & HASTE
Neutron
Spacecraft Family
Space Systems
Space Services
Global Facilities Tour
Leadership & Governance
Conclusion
Thesis
I believe Rocket Lab’s current share price is not accurately reflective of the company’s future prospects and the high probability that it achieves those prospects. With that said, I should clarify here - this investment has virtually 0 margin of safety and represents more of a bet on the future of commercial spaceflight and management’s execution than a trade based on short term fundamentals. If that sort of thing isn’t for you, it’s best not to consider Rocket Lab, as they are not set to be profitable until 2026 *at best*.
Since founding in 2006, Rocket Lab has grown from a small-time launch provider into an absolute maverick of an end-to-end space company. They run highly aggressive schedules and have a well-earned track record of on time delivery, consistent execution, and extreme precision, unrivaled in the aerospace industry. Rocket Lab has ousted players like Boeing, Lockheed, and Raytheon, and is taking more deals as a prime or sole contractor, simply because they have the capability to do almost everything an aerospace customer needs in house, on budget and on time, with consistency. This combination of factors was completely unprecedented until Rocket Lab arrived on the scene. I expect Rocket Lab to continue outcompeting its peers in this manner, and for the company to be rewarded accordingly.
Rocket Lab is poised to capture a large market share in 3 rapidly growing space subsectors: Launch, Space Systems, and Space Services. The TAM outlays here are: Launch, $10bn. Space Systems, $20-30bn. Space Services, $200-300bn. Of course, estimates vary and these are rough estimates at that, but this can give you an idea of the risk/reward here, as today Rocket Lab is worth about $3.5bn.
Rocket Lab is already dominant in small launch with their Electron rocket and they are rapidly developing a competitor to SpaceX’s Falcon 9 in medium launch called Neutron. If they do not end up dominant in medium launch, they will almost certainly be #2 behind SpaceX, which is not a bad place to be.
Rocket Lab has broken countless records in rocket development and are known for their low program costs, relatively fast development and scaling, and reliability above all else. They are a trusted and premier launch partner and satellite components supplier with an extremely impressive track record of proven reliability, precision, and efficiency across all their business lines.
My cost basis for RKLB is $5.04, and I fully expect this to come down sometime or another. There are not really any easily discernable catalysts to move this stock before the first Neutron launch, which is currently expected in mid 2025. Almost annoyingly, as I’ve been writing this article over 3 weeks, the stock price has gone up some 40%, so these price targets are gonna look a little funky for now.
Short term PT: $5-7
Medium term PT: $8
2030 PT: $30.10 - ~25% CAGR
Risk Factors
New entrants and competition may negatively affect Rocket Lab’s market share in small and medium launch, and in space systems and space services.
The possibility of an Electron launch failure is unlikely but ever-present, and this would damage Rocket Lab’s credibility somewhat.
If the Neutron development timeline is pushed back further from a mid 2025 launch, the company’s profitability will likely be delayed accordingly.
Early Neutron launch failures will set the Neutron program back accordingly, and delay profitability, again.
If Rocket Lab fails to provide an offering to the Space Services market, say a communications constellation, their potential TAM will shrink massively.
The biggest and most lurking left-tail risk with anything related to space travel is not profitability - it’s Kessler Syndrome. You know, for space travel and everything else. But that’s not gonna happen any time soon right! I’m only half joking.
There is a (very, very low) probability that Rocket Lab spacecraft components may fail in flight, this would damage the company’s reputation.
It is extremely difficult to estimate the future TAM for Space Services specifically, and this poses some risks because growth in Services means growth in Launch and Systems as well.
Rocket Lab is not profitable and may need to raise further capital to finish development of their Neutron rocket, or for further M&A opportunities.
Before we launch into the analysis behind the thesis, I’d like to note that I’ll be primarily comparing Rocket Lab to SpaceX on Launch, and to legacy competitors like Boeing, Lockheed and Airbus for Space Systems.
The methodology is, no other competitor in the launch business presents a legitimate threat at this point. SpaceX is the obvious #1, Rocket Lab the obvious #2. For Space Systems, comparisons get a little trickier.
Until SpaceX and Rocket Lab came along, the entire industry was dominated by outsourcing and subcontracting with cost-plus contracts put up by huge government agencies (think NASA) for a select few legacy companies like Lockheed or Boeing. One could argue this breeds inefficiency, given that any private contractor has no incentive to spend less, as their costs are getting covered no matter what plus some profit margin. SpaceX and Rocket Lab did not have this privilege, thus their survival was dependent on rugged innovation and cost efficiency above all else. They did not have another option - it was quite literally a game of “reach orbit or die trying.”
What SpaceX and Rocket Lab have done is extremely impressive given this constraint. But today, only one of these companies has a hand in Space Systems, and that’s Rocket Lab. Rocket Lab is the first company to vertically integrate enough different components to be the sole contractor on an entire mission - designing a satellite, building it, launching it, and then operating it on orbit, all in house. This should give Rocket Lab much higher gross margins than competitors on its satellites and components, given they rely on very little (if any) subcontracting. It also makes it far, far easier for Rocket Lab to build and launch a constellation of their own, because they own all the components of that. SpaceX has to buy payload separators from Rocket Lab - Rocket Lab can make any components needed for their own constellation, and Amazon’s, and many others. Rocket Lab is also able to outcompete the legacy players in Space Systems on cost and delivery time, and they are taking more deals as a prime or sole contractor because of this.
Notable Missions & Contracts
Despite being such a scrappy underdog in the space business, Rocket Lab has demonstrated an extremely impressive track record of mission success for a wide variety of customers. This list also features Rocket lab’s signature mission titles:
Launched and guided CAPSTONE to a unique lunar orbit for NASA’s Artemis program.
Designed and built two Mars orbiters in partnership with NASA and UC Berkeley for the ESCAPADE mission, to be launched aboard New Glenn in late 2024.
Facilitated the first commercial in-space manufacturing venture for Varda, using the Photon spacecraft bus to operate Varda’s factory capsule on orbit for 8 months before landing the payload in the Utah desert for recovery. They are contracted to provide Varda with 3 more Photon spacecraft to date. Varda’s capsule uses the unique low-g environment of Earth orbit to grow ritonavir crystals, a drug commonly used to treat HIV. Certain crystal structures and compounds grow differently in low-g environments, leading to a lot of potential for in-space manufacturing growing forward.
Subcontracted in 2022 by MDA (formerly MacDonald, Dettwiler, and Associates) to design and build 17 spacecraft buses for the new Globalstar constellation, for $143mm in revenues, with deliveries beginning in Q1 of 2024.
Launched numerous “spy satellites” (classified payloads) to orbit for the DoD, trusted with the foremost national security concerns.
VICTUS HAZE mission booked for the US Space Force; Rocket Lab is contracted to design and build a satellite solely from Rocket Lab components, then launch it within 24 hours notice from the USSF. This satellite is designed to demonstrate rapid response capability, but has a secondary objective of orbital rendezvous with a simulated “threatening spacecraft.”
Two launch missions in May and June of 2024 entitled ‘Ready, Aim, Prefire’ and ‘Prefire and Ice’ saw the launch of two climate satellites into polar orbit within 3 weeks for NASA’s PREFIRE mission, studying how heat leaves the Earth through the poles.
Two launches in May 2023 for NASA’s TROPICS climate satellites studying hurricane and tropical storm development, entitled ‘Rocket Like a Hurricane’ (my personal favorite) and ‘Coming to a Storm Near You’. This launch contract was originally meant to be fulfilled by small launch competitor Astra before their rocket suffered a continuous spate of launch failures and was subsequently scrapped, taking the first two TROPICS satellites down with it. Back-to-back launch missions like this and the former play to Rocket Lab’s strengths as a high cadence, high turnaround launch provider - no competitor in small launch has this kind of capability.
Launched and rendezvoused a satellite with a derelict rocket stage for Astroscale Japan, an extremely impressive accomplishment that demonstrates orbital rendezvous capability.
Awarded $515mm prime contract to design and develop 18 satellites for SDA’s (Space Development Agency) proliferated joint war fighter constellation tranche 2. Rocket Lab’s vertical integration allows them to build almost the entire satellite in-house, including solar panels, structures, star trackers, reaction wheels, radio, flight software, avionics, and launch dispenser. The only thing they need subcontractors for is payload systems for these satellites. This contract will be carried out by Rocket Lab National Security, a subsidiary created specifically to address national security and defense needs from world governments.
Business & Financials
Rocket Lab went de-SPAC in late 2021, raising $777mm gross proceeds. From the chart alone, you can derive that Rocket Lab is different from other SPAC(e) stocks, such as Astra Space (delisted after $0.5/share take-under) and Terran Orbital (recently acquired by Lockheed at $0.25/share).
Rocket Lab’s business is split into two segments: Launch and Space Systems. Launch makes up around 1/3 of the company’s revenues, with Space Systems being the other 2/3. I will explain both of these operating segments in detail in their own sections.
The chart below demonstrates topline growth and gross margin improvement since 2019:
Q2 Earnings Highlights:
$106mm in quarterly revenues, a record, up 71% from the year ago quarter.
$29mm in revenue from Launch, $77mm from Space Systems.
Revenue up 15% QoQ.
$27mm in gross profits, 25.1% GAAP gross margins, up 2.1% from the year ago quarter.
$40mm in R&D expense, $30mm SG&A, and $15mm in capex.
Backlog at $1.067Bn, up 5% QoQ. They expect to recognize 44% of this backlog within 12 months and the remaining 56% beyond 12 months.
100% increase in launch cadence from 1H 2023 to 1H 2024, launches expected to be up 60% YoY in 2024.
Completed Archimedes engine hot fire testing at 102% throttle.
Rocket Lab is on pace to grow revenue by 73% this year to $418mm, if you take the midpoint of their Q3 guide and assume Q4 sees an even 1/3 split of remaining backlog recognition through Q2 2025. They are seeing massive growth in both Launch and Space Systems, as the fruits of their investments into these markets begins to ripen.
Now, to address the chimpanzee in the space station: Rocket Lab is far from profitable and will remain so until 2026 at best. CEO Peter Beck estimates that Rocket Lab will achieve FCF profitability two quarters after the first Neutron launch, which is currently expected in mid 2025.
On $51mm of gross profits last year, Rocket Lab saw operating costs of $229mm, resulting in a $177mm operating loss. Most of this spend is to support Neutron’s development, around $40mm a quarter as stated by CFO Adam Spice. We should expect to see a large reduction in capex as well as Neutron associated R&D expense after Neutron’s first launch and further cost decline as the program spools up into 2026. Further program costs will be offset by Neutron booking $60mm launches with cadence increasing dramatically in the years after its first launch. Really, their medium term profitability is dependent on Neutron’s success and declining Neutron spend following that. Rocket Lab has enough cash runway to reach profitability assuming there are no further Neutron delays (Neutron was delayed by 6 months last year from an end-2024 launch to a mid-2025 launch).
Recently, Rocket Lab raised around $300mm net proceeds through a convertible notes offering, with funds expected to be used for strategic M&A opportunities in spacecraft payload systems. With this capital raise, Rocket Lab entered into a $40mm capped-call transaction that could partially or fully offset share dilution from the raise, depending on stock price movements through 2027 when notes become redeemable.
Below is my model for Rocket Lab out to 2030, taken by adding the estimated gross profits of both business lines, assuming net income margins in the low 20s, and slapping a 25x multiple on it. I’ll explain my results and my assumptions below:
Assumptions:
Launch:
Both launch sections have a recovery % metric, an approximate percentage of rocket stages recovered out of total launches during that year. This data feeds into the variable cost/launch (cost to build the rocket) functions for Neutron and Electron, pinned on two pieces of commentary from management: 60% of Electron’s production cost can be saved with recovery, and close to 50% of Neutron’s. In both cases, the more expensive part of the rocket is the non-recovered part, the second stages.
My model accurately reflects these variable cost assumptions out to 2030, assuming a 50% terminal Electron recovery rate and 91% for Neutron. If anything, my Electron model is wildly undershooting, because management has commented that 22 Electron launches/year is profitable at 50% GM - my 2025 estimate with 24 launches is half that gross margin.
Data on Electron’s average selling price is pulled from those years’ respective 10-Ks, but increases by 2.5% per year after 2023 to account for inflation as management has guided. Neutron is assumed to begin at a $55mm sticker price, which also increases 2.5% per year to account for inflation.
On launch cadence, we assume 16 Electron launches in 2024 which should be conservative, which is a 60% growth rate. I am assuming cadence growth declines 10%/year past 2024 until bottoming at 20% growth to 2030, with 78 launches estimated for that year. This more or less tracks against Falcon 9 data - it took F9 5 years to go from 18 launches/year to 56 launches/year, I estimate Electron goes from 24 launches in 2025 to 78 in 2030. A little higher Electron growth, but Electron beat F9 to 50 launches and is on track to beat it to 100 launches as well so I feel it’s warranted.
For Neutron cadence, Rocket Lab has stated that they like to follow a 1-3-5 annual cadence structure after a first successful launch. Neutron’s first launch is expected in mid 2025, so 1 launch that year, 3 the next, 5 after that, and from there cadence grows to fully fill the 12 Neutron launches/year cap set by Neutron launch pad LC-3 (see Global Facilities Tour).
2021-2023 Electron avg cost/launch is taken from those years’ respective 10-Ks. Electron’s variable cost in 2021-2023 is from an interview where CFO Adam Spice mentioned the materials cost of an Electron is around $5.5mm. Using provided values of materials cost and avg cost/launch, I calculated an estimation for fixed costs/launch for 2021-2023. In 2024E, this metric is pegged at $1mm, and Electron’s variable cost/launch decreased to $4.4mm to accommodate data from the Q2 2024 10-Q, which states an avg cost/launch of just $5.4mm (I’m going to assume this value for the full 2024E). Beyond 2024, fixed cost/launch increases 2.5% per year to account for inflation, and variable cost/launch decreases beyond 2024 according to the recovery metric.
Management has expected that Neutron gross margins will end up in the 50% range when at proper cadence, so I assume each vehicle costs $25mm to build.
Space Systems:
This segment is pretty hard to model as Rocket Lab doesn’t release pricing or quantity data for their spacecraft components. Here, I used the Q2 2024 backlog and their expected revenue recognition rate of that backlog into 2025 to estimate 2024 and 2025 revenue, from there assuming a target % growth per year that drops off into 2030.
I assume a 30% gross margin for Space Systems into 2030, which is management’s target for that business line, and Systems margins are currently a little over 31%. Launch gross margins are calculated individually by year, using my estimates for price, avg cost/launch, and cadence.
Overall:
My estimated 22% net income margins in 2030 fit with management’s target operating margin in the high 20s, and my calculated 2030 gross margin of 41%.
I expect 2024 ending shares outstanding of 500 million, up 6 million from Q2, and I expect further dilution of 4%/year through 2030.
Results: This model expects 2030 revenues of $3.46Bn at 41% gross margin, and net income of $761mm at 22% net margins. 2030 shares outstanding are estimated at 632 million, leading to EPS of $1.20 in 2030. Given that they’d be growing gross profits at 29% in 2030, I’ll apply a solid growth multiple of 25x to 2030 EPS to determine a stock price of $30.10, around a 25% CAGR from these prices. I also believe Rocket Lab may end up trading with a solid premium built in, I’m thinking of calling it the “this company is publicly traded and can land rockets like SpaceX” premium as I fully expect people to lose their marbles when Neutron lands successfully for the first time.
Launch
The pre-2022 “free money” environment resulted in a lot of new launch startups, and with them came a lot of fantastical claims and unattainable deadlines being thrown around in the launch scene. CEO Peter Beck has mentioned that at one point, he could count around 140 startups working on launch capabilities - I imagine that number has shrunk by quite a bit now. As cheap capital has dried up, so too has investment in space, and many of Rocket Lab’s so-called competitors are now on life support.
Billionaire-backed Virgin Orbit declared bankruptcy in 2023 after their air-launched rocket failed to demonstrate reliable orbital capabilities. Astra Space went public via SPAC in 2021 valued at $2.6Bn, and earlier this year its cofounders threw out a take-under at just 50 cents per share, what they called “the only alternative to chapter 11 bankruptcy.” With the completion of the take-under, Astra was valued at just 13 million dollars in market capitalization. Rocket Lab may be down 40% from its de-SPAC price, but it could be like, so much worse.
Even Lockheed and Boeing want out, as they are reportedly in talks to sell their joint-venture ULA to Sierra Space, of all people. FYI, I love Sierra, I just wouldn’t have expected them to bid for ULA as they are developing their own reusable spaceplane called Dream Chaser (it’s every bit as cool as it sounds and I wish them the best).
Don’t even get me started on the Boeing Starliner fiasco that has left astronauts stranded on the ISS and as of 8/24 is expected to return uncrewed - in comparison, SpaceX’s Crew Dragon capsule has performed nearly flawlessly since it was introduced. At this point, what else do we expect from Boeing, really?
Currently, SpaceX and Rocket Lab are the only real players at the poker table, and I made the following graphic to emphasize that:
Some notes, I include partial failures as full failures in the Reliability %, excluding booster recovery failures. Any values with * after them are uncertain due to a number of factors - it’s difficult to find exact program cost estimates for most of these as a lot of rocket programs tend to iterate on previous designs or include technology not developed in-house, or they just don’t publish anything. For 2023 and 2024E cadence, I include only commercial launches bearing payloads for customers, but the total launches section includes all launches of a vehicle regardless of the customer. For vehicles meant to be reusable, the payload capacity used is from reusable vehicle variants.
At this point, Rocket Lab has no legitimate competitors in dedicated small launch and Firefly, the arguable runner-up, is not even remotely close. Rocket Lab’s utter lack of competition in small launch can be explained by an age-old saying in the space community: space is hard. It’s really, really goddamn hard. Designing and building a rocket is an engineering feat in itself, but after that, you need to put that rocket on the pad and fly it to orbit as soon as you possibly can. As Ashlee Vance said in his book When the Heavens Went on Sale, “It is at this point in every new rocket program where things keep going wrong for an extended period of time.”
Rocket launches can fail for an infinite number of reasons, especially the earliest launches. The more launch failures you accrue, the more cash you burn with no revenue to show for it and the less likely it becomes that someone will put their satellite on your rocket for future launches - SpaceX’s first orbital launch of Falcon 1 flew a mass simulator instead of a live customer payload, as nobody trusted them to reliably deliver at that point after 3 previous failures.
CEO Peter Beck says that if launching his first rocket was hard, launching his 20th rocket was hard squared. It is impossible for a new startup to anticipate all the manufacturing snarls, supply bottlenecks, and testing failures they are inevitably going to accrue before their first launch, much less their 20th launch. In other words, the manufacturing and logistics side of high-cadence launch is much harder than actually launching a rocket, which is once again an insurmountably difficult task in itself. Rocket Lab isn’t where they are today because they got lucky, they’re here because they beat the odds - they worked hard enough, fast enough, and cheaply enough to get their rocket program off the ground before they ran out of startup capital, and the same cannot be said for any of their competitors in small launch, even those who started with a lot more capital.
Enough about the general launch market, let’s get into the real meat and potatoes, shall we? Time to talk about what really makes Rocket Lab different, the legendary Electron launch vehicle.
Electron & HASTE
Rocket Lab’s workhorse launch vehicle, Electron, is a carbon composite smallsat launcher with a sticker price of $7.5mm for ~340kg to LEO. Electron is a pretty small rocket - tiny in fact, compared to SpaceX’s Falcon 9 and even some of its competitor rockets in small launch. Despite its small stature and low price tag, Electron punches well above its weight:
third most frequently flown rocket globally
64% of US non-SpaceX launches are Electron
52 missions to date and counting, 92% success rate - 2024 launch cadence expected to be up 60% from 2023
Secured launches for NASA, the NRO, DARPA, US Space Force, and a rapidly growing commercial customer base
Electron saw the lowest development cost ever for a comparable size class rocket - beating out the better funded Falcon 1 by an inflation adjusted 8 million dollars. For more accurate comparison, Electron has similar payload capability to LEO and SSO while being a little smaller and a lot lighter than the Falcon 1 thanks to its carbon fiber structure. Electron also made orbit and deployed 3 commercial cubesats on its second ever launch - it took SpaceX four launches to make orbit with Falcon 1.
It is also the fastest commercial rocket ever to reach 50 flights - even beating out the much larger Falcon 9. It took Rocket Lab just 3 years to launch Electron for the first time, starting from nothing.
All these accomplishments are much more impressive given Electron’s size. In trying to make rocketry profitable, size matters quite a bit. For one, the fixed costs of a launch typically don’t increase much with a larger rocket. The 5 or 10 person launch safety team for Electron doesn’t need to be 43x larger for Neutron just because Neutron’s payload capacity is that much larger. The sticker price of Neutron will be $50-60mm, around 7x Electron’s price, so amortizing the associated launch expenses over the revenue recognition cycle will be a lot easier with that higher sticker price. Essentially, cost absorption is the key to profitability in a launch business, and it’s made much easier with a higher price tag per launch. SpaceX kind of abandoned dedicated small launch with the discontinuation of the Falcon 1 in favor of the 9 - they didn’t think it could be made profitable so they moved up, where it’s far easier to amortize launch expenses. Rocket Lab is turning the corner on small launch profitability with Electron, which nobody thought was possible a decade ago.
Now let’s talk about $/kg ratios. The $/kg ratio expresses the dollar cost of 1 kilogram to LEO. Electron’s is $22,000, whereas a reused Falcon 9’s is $4000, steeply cheaper. So why does anyone choose to launch on Electron? Flexibility.
The vast majority of Falcon 9 launches are for StarLink, but those that aren’t are usually rideshare missions, where many small satellites can ride along in the same payload fairing to reach orbit. Falcon 9 has managed 100+ satellites deployed in a single launch, which is pretty nuts. Electron could never do that, and it costs a lot more /kg, but there are more dynamics at play here.
For one, a SpaceX rideshare drops all the satellites off in the same spot, the same orbit. Many of these satellites then have to spend weeks or months carefully maneuvering to their target orbits, spending much-needed propellant and wasting a lot of time just to finally begin their operations. Second, the available launch slots for these rideshares are few and far between, typically being booked 18 months or more in advance. Electron completely negates both of these issues. Customers can call up Rocket Lab and have their satellite delivered to a perfect orbit within a measure of weeks - that’s unheard of.
Electron essentially offers a premium service that small launch customers are more than happy to pay extra for, because it means their satellites can get to space a year and a half earlier and start generating revenue immediately. If they don’t need to waste propellent navigating to their desired orbit, they can stay in space longer too. Electron also offers a “smoother ride” as CEO Peter Beck puts it, pulling a cool 3gs on average up to orbit with lower fluctuations than competing rockets.
Electron only costs $7.5mm and that’s really not a lot. Some of you reading this could book an Electron launch and put 325 kilograms of whatever you want into space. For any given launch, the spacecraft itself could cost in excess of $20mm, so launch is almost never the more expensive component. By making dedicated small launch affordable and accessible, Rocket Lab has enabled loads of companies to get their satellites in orbit sooner and with more precision than ever before, helping to create the market they’re selling launch into as these companies now have good reasons to keep launching.
Before Electron, the price for 200kg to LEO was 35-50mm because launch vehicles were simply larger in size, and no dedicated small launch vehicle existed so customers were forced to pay for space they didn’t need on larger rockets. Electron has got the cost for 340kg to LEO to just $7.5mm, extremely impressive stuff and truly revolutionary for the small launch market.
I should mention, Electron also has rideshare capabilities. I think their record was 33 smallsats deployed from a single launch, which is definitely not bad! Electron is quite customizable too, with multiple launches featuring custom fairings to better fit a customer’s payload. The below example is one of their launches for Synspective, a Japanese SAR Earth imaging company. Synspective signed a deal for 10 Electron launches over 3 years not too long ago - they are choosing Electron to deploy their entire constellation, $/kg ratios be damned, because of its flexibility.
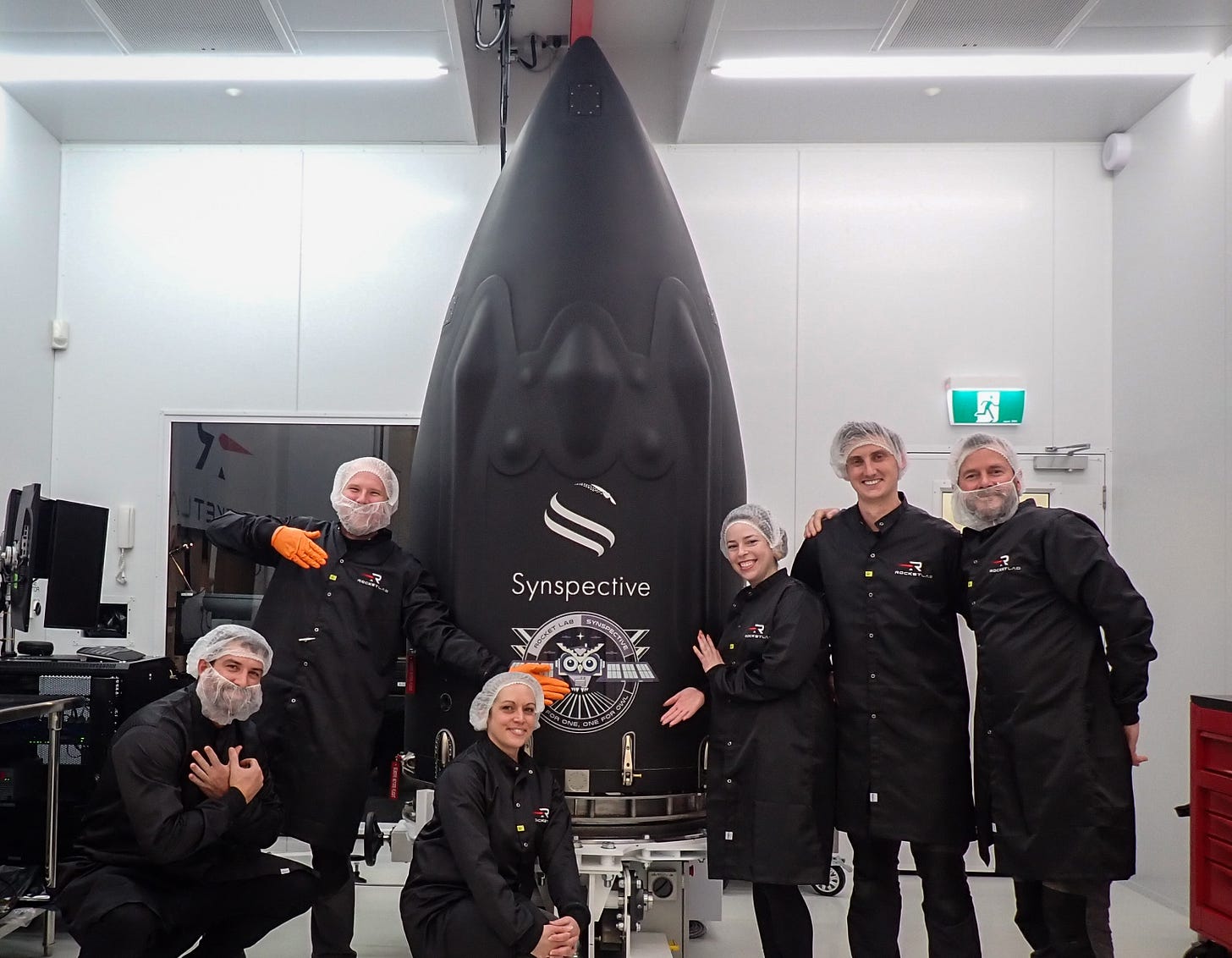
Many customers like Synspective plan and build out their constellations specifically for the Electron platform, which means they’ll choose Electron for constellation replenishment once their existing satellites eventually retire, like replacement revenues.
Electron’s orbital insertion precision is genuinely cracked, all thanks to its Photon kick stage. This kick stage put a satellite in a unique, first-ever orbit around the Moon for the Artemis program, is expected to be able to reach Venus, and will take two orbiters to Mars later this year. On launch 50, Photon deployed a payload of 5 IoT satellites for Kinesis within just 8 meters of the target. Not 800, not 80, 8. Many of you won’t understand how nuts that is for a commercial company, but the typical margin of error for these deployments is 15 kilometers - when at orbital speed and rapidly accelerating, the incremental burn of even milliseconds extra can add kilometers to your final destination. This level of accuracy on a mission like this is essentially just showing off, but it demonstrates the extremely sought after capability of orbital rendezvous, the meeting of two spacecraft in orbit. This capability is not just crucial to ISS operations, but necessary for future space junk removal campaigns and perhaps advanced spying or satellite warfare by the DoD (I’m not kidding - see Notable Missions & Contracts).
On launch 47, a Photon-assisted Electron deployed an observation satellite for KAIST at 520km, then deployed a solar sail test satellite for NASA at 1000km, in a totally separate orbit. This capability is also kinda unheard of from any other launch provider, commercial or government. What’s crazy is, even after these two deployments to completely different orbits 500km apart, the kick stage had enough fuel left to lower its orbit far enough down to de-orbit much sooner.
For launch 27 ‘On Closer Inspection’, Electron launched a Photon-assisted satellite to rendezvous with a derelict rocket stage for Astroscale Japan. This 150kg satellite will fly around the rocket and gather data, attempting to determine how such objects could be captured and de-orbited in the future. Orbital rendezvous is hard, but rendezvous with a non-cooperative object like a derelict rocket is absurdly hard - you have no precise relative velocity and no spin measurements on the target craft until you get near it, and extremely tight orbital parameters. Rocket Lab was delivered the final orbital parameters just 20 days before launch, and their exact takeoff time was only defined the day prior to launch with a margin of error of just 15 seconds.
Electron is somewhat unique in that it leaves very little orbital debris, if any. The first stage doesn’t make orbit and will either be recovered or crash into the sea. The second stage is cut off just before it would make orbit and burns up in the atmosphere. The third stage, the Photon kick stage, can de-orbit itself after deploying a payload, so that only the satellite is left in space. This is pretty important, as the majority of space debris today is just spent rocket stages, and Electron totally avoids this issue.
Electron made a few rocketry firsts with its creation, one being the first use of an electric-pump-fed engine cycle and another being the first use of an engine with 3D printed primary components. Powering Electron’s first stage are 9 Ruthorford engines, 3D printed out of inconel superalloy. These engines burn RP-1 and LOX (refined kerosene and liquid oxygen, also called Kerolox) without the need for a gas generator to spin the engine’s turbopumps, instead using about a megawatt of battery power over 160 seconds. This presents some positives and some drawbacks - for one, getting around using a gas generator allows Electron to “suck the tanks dry”, burning all its available fuel in the combustion chamber because it isn’t using any to spin the turbopumps. This results in higher specific impulse of 311s at sea level and 343s in vacuum - not bad for either stage. The drawback is that the batteries add extra weight to the first and second stages. To mitigate this somewhat, Electron’s second stage will “hotswap” from two batteries to one halfway through its burn, switching the power draw over in real time while the engine is burning, and jettisoning the two drained batteries to burn up in the atmosphere.
One neat advantage with this approach is that as battery technology has improved, Electron’s payload capacity to LEO has grown because each battery mass reduction flows straight through to extra payload mass potential. Payload capability started at 225kg to LEO and as of the latest improvement stands at 340-350kg to LEO. They have also made great strides in the reuse of these batteries. As you can imagine, drawing a megawatt of power within 160 seconds doesn’t typically bode well for your battery - that amount of energy could power hundreds of homes and it’s all coming from a few chunks of lithium polymer. Electron’s batteries had a tendency to “turn themselves inside-out” after this massive draw, needing to be replaced after a single flight. But Rocket Lab has since developed batteries that they believe they could get 10 flights out of after recharging, which will save a lot of money and greatly enhance Electron’s reusability campaign.
Speaking of - Rocket Lab has made great efforts on Electron reusability, which they estimate will save them 60% of the cost of Electron’s first stage. To this end, they have tried catching Electron with a helicopter, which actually did work - but catching such a big load understandably spooked the pilots, and helicopters can’t fly when it’s rainy out, which it often is when you happen to be trying to recover rocket stages. Instead, Rocket Lab now seems to be opting for parachute-assisted splashdown going forward. Though the rocket will be exposed to corrosive saltwater on splashdown, the 60% cost savings estimates still apply. So far, we have seen hot fire tests of recovered engines and Rocket Lab is looking to launch the first recovered Electron first stage as soon as 2025, though they have wound reusability efforts down for the time being, to direct more resources to Neutron’s development.
Electron has launched 52 times and counting, with a 94% “adjusted” success rate so far - 48 successful launches and 4 failed missions. Three of these failures are quite reasonable, in that the chances of their root causes occurring were minuscule and it would have been extremely difficult to weed out anomalies like this during regular testing. The other mission failure was literally their first ever Electron launch, and the issue was actually with ground-based range finding systems used by 3rd party American “babysitters”, not the rocket, not any Rocket Lab systems. Nevertheless, the vehicle had to be terminated and the mission deemed unsuccessful. The rocket was performing exceptionally and almost certainly would have reached orbit, so I’ll adjust the success rate to 94% - 49 successes and 3 failures. But a 94% success rate is really quite good, at least compared to the rest of the US launch scene right now, SpaceX excluded.
Rocket Lab has set up Electron contracts so that 90% of the revenue for a launch is collected in increments before the launch, with the final 10% being collected upon engine ignition and liftoff. They use two different billing models, as seen below. Rocket Lab has also stated that they price Electron depending on how much handholding a customer needs. If a customer can just toss Rocket Lab their payload and let them handle everything else, they should expect around a $7mm cost for launch as opposed to the $7.5mm sticker price. When a customer requires more frequent updates or strict national security measures to be taken, say for a DoD launch, the cost of launch can increase to over $14mm. They have also stated that they will increase the base $7.5mm sticker price by 2.5% per year to account for inflation. Also, I should mention that there is an insurance market for these launches, so launch failures are not the end of the world on the customer side, more of an occasional and expected hazard.
HASTE:
When the Pentagon’s hypersonics director Mike White called for an increase in hypersonic test launch cadence, Rocket Lab responded with haste - literally. The Hypersonic Accelerator Suborbital Test Electron (HASTE) is a suborbital Electron variant used for hypersonic and high altitude testing.
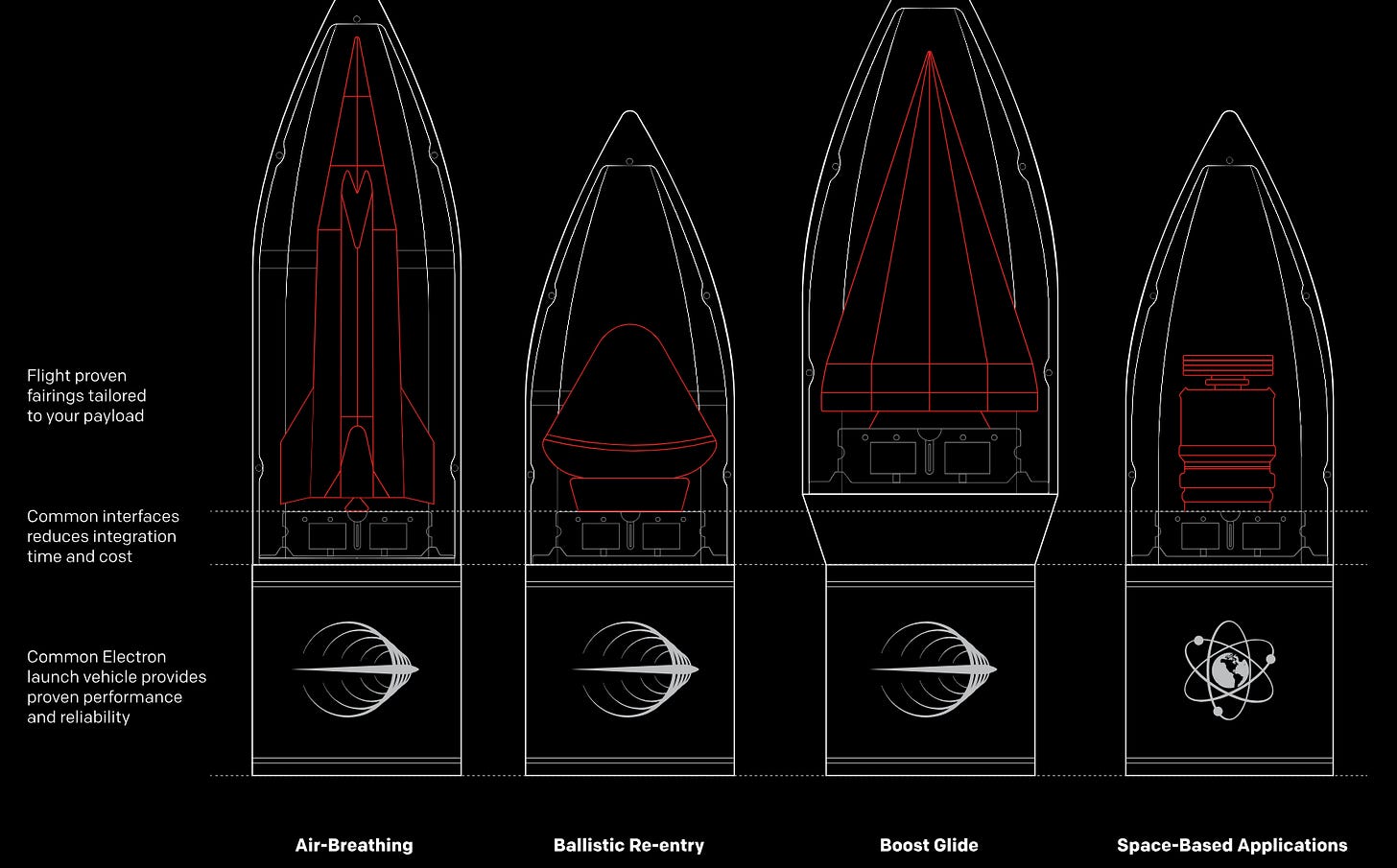
Hypersonic testing is necessary to design anything that returns from space or operates at high speed and/or high altitude, from heat shields and capsules to advanced new-age airfoils. This testing is in high demand from the cutting edge of aerospace operators and large government organizations alike. Typically, these kinds of tests are run in large wind tunnels or vacuum chambers, but even still, recreating the aerodynamic and heating environment of Earth’s atmosphere while on solid ground is extraordinarily difficult and cost prohibitive. The best wind tunnels and vacuum chambers cost quite a bit to run and have few slots available, as there are not many of them and demand is very high. And if it was up to you, would you rather test your new-age spaceplane in a hypersonic wind tunnel or in a real hypersonic environment, deployed at 80% of the distance to space and traveling at 7.5 kilometers a second?
One customer, Leidos (LDOS), has already chosen the latter, booking four HASTE missions so far. These missions cost a little more than a traditional Electron at around 10mm per. Using a modified third stage, HASTE can carry 700kg to a variety of altitudes, velocities, and trajectories. 7 more HASTE missions are currently booked on the launch manifest, another $70mm in revenues. These hypersonic tests have a TAM of around $1bn, according to NASA and DoD budgetary outlines.
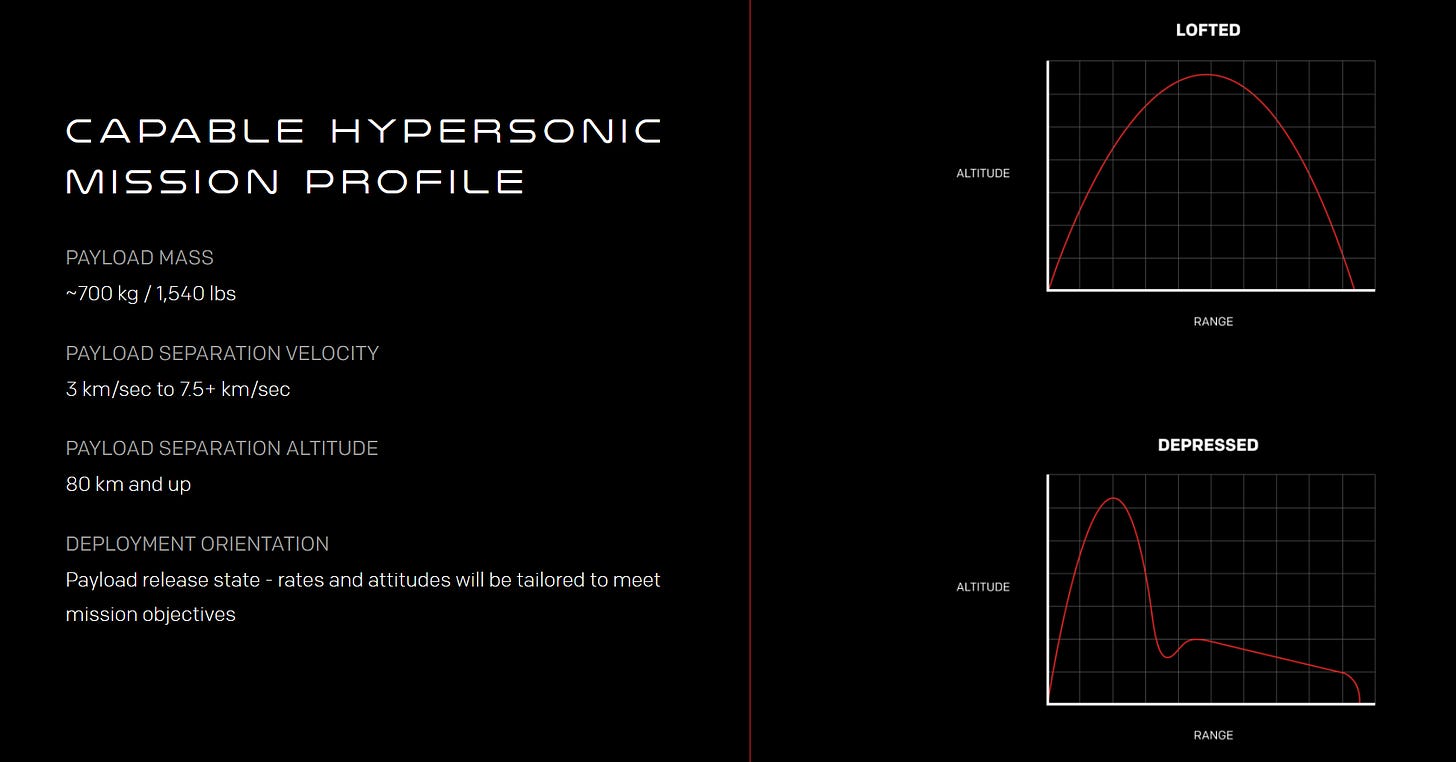
Neutron
Neutron is an upcoming medium launch class rocket under development by Rocket Lab, for two primary reasons: Breaking SpaceX’s launch monopoly and launching constellations faster and cheaper than anyone else. At its current projected launch date, Neutron is poised to beat the Falcon 9 to first launch by half a year.
And to beat Falcon 9 (expendable) in development cost by an inflation adjusted $250mm. It’ll beat the reusable Falcon 9 by around $1.6Bn, and keep in mind, Neutron is meant to be a reusable rocket.
Neutron’s fundamental design should allow it to outclass the Falcon 9 in cost, weight, reusability, and launch turnaround. Neutron will be a fully carbon fiber return to launch site vehicle with payload capacity of 13,000kg to LEO, powered by a first stage of nine Archimedes engines and a second stage of one vacuum-optimized Archimedes engine. The current design features a fully integrated payload fairing, complementing reusability and turnaround time, among numerous other efficiency improvements:
Key Design Aspects:
Carbon composite fuel tanks and structural panels, around 25% the weight of stainless steel for similar performance under load. Carbon composites are also naturally resistant to buckling loads, allowing Neutron to go without a lot of the internal tank support structure seen on other rockets, saving further weight.
Aerodynamic control through re-entry will be provided by 4 canards fixed near the top of the rocket. The Falcon 9 uses 4 grid fins, which must first fold out before they can rotate and provide control, which is 2 axis of rotation and double the failure points of Neutron’s canard design. These canards will remain fixed during ascent, where engine gimbal will be the primary control input.
The rocket body is sloped to be fatter at the bottom and taper off at the top, which helps it shed aerodynamic force during re-entry. Because of this and the fact that Neutron essentially weighs nothing, it will not require a re-entry burn to slow down before hitting the atmosphere, saving much needed fuel for the landing burn and allowing for an increase in payload capacity.
Features 4 permanently mounted, extendable landing legs designed to absorb shock on landing. These legs extend up the body of the rocket and act as raceways, protective covers for plumbing and wiring. Two of these legs extend further than the others, designed to act as lifting bodies during re-entry.
Fully integrated two part payload fairing, dubbed “Hungry Hippo.” Typically, fairings are kicked off when the payload is deployed and are not recovered. SpaceX tried to catch fairings with parachutes and ships equipped with giant nets, but ultimately abandoned the concept. Neutron’s fairing instead will be permanently affixed to the rocket, opening up like a flower petal to deploy Neutron’s second stage, before closing again for re-entry. This will allow Rocket Lab to save a considerable amount of money on fairings, and a good chunk of time on payload integration.
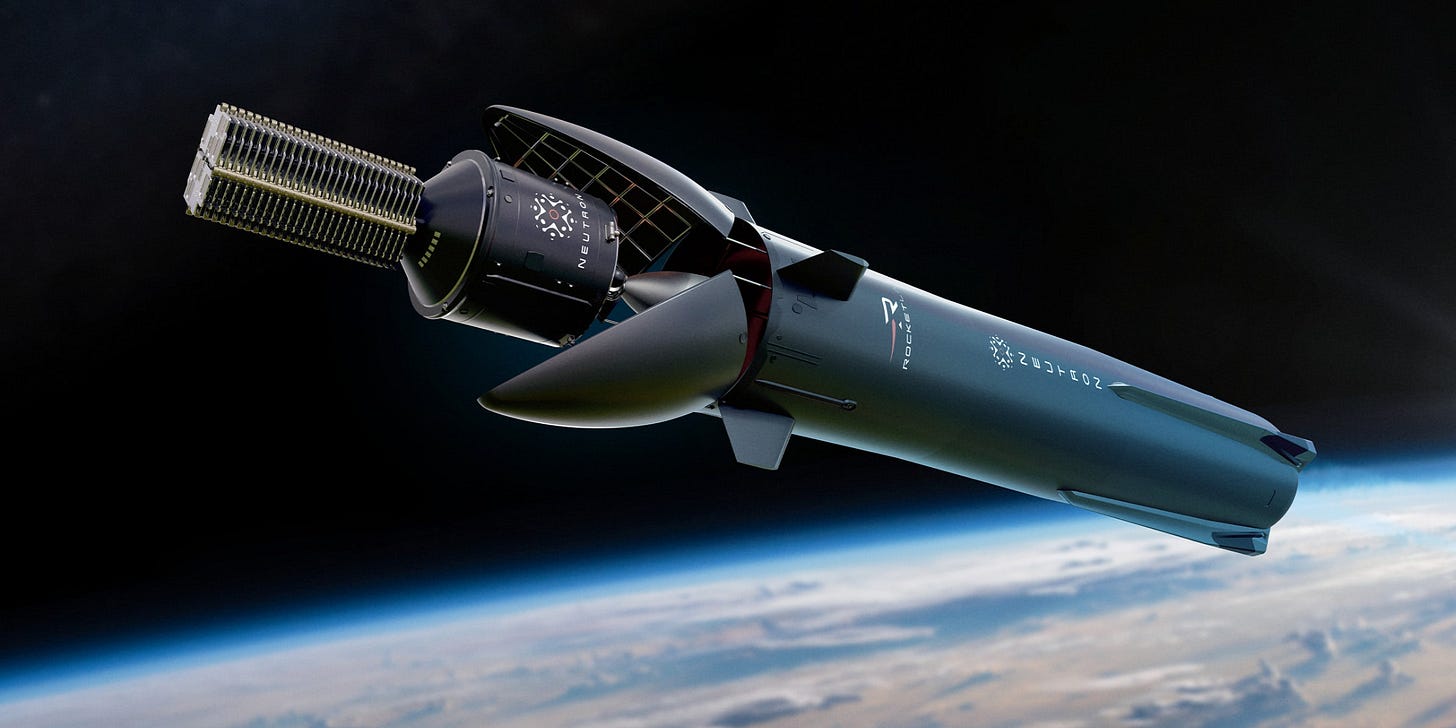
Neutron is designed to land vertically at it’s launch site, not on a drone ship like a Falcon 9 (though, this capability will be made available to some customers who want the extra ~5 tons of payload capacity). This will cut into its kg/orbit slightly but dramatically simplifies the booster recovery and reuse process. The Falcon 9 boosters that land on drone ships must be loaded horizontally onto a truck and hauled back to a SpaceX facility from the coast. This was a key design constraint of the Falcon 9, that it must be thin enough to fit down U.S. highways. Neutron does not need to deal with this constraint, thus it can afford its tapered shape, with a fatter bottom. Not to mention, Neutron (on return-to-launch-site, RTLS missions) can avoid the absolutely immense costs associated with operating drone ships and transporting rockets hundreds of miles over land. The rocket is designed to land vertically at its launch site, be carried back to a bay vertically, with vertical payload integration and immediate re-launch capability without the use of a strong back, the mechanism that raises the rocket from a horizontal to vertical orientation on the launch pad. Eliminating the strong back saves further time on re-launch and eliminates some unnecessary launch pad complexity. The umbilical fuel lines will be connected to the base of the rocket as opposed to its side, the typical configuration for launches with a strongback. I should also mention, the first few tests of Neutron will be barge landings, they’ll have to nail that before attempting to send what is essentially a giant self propelled bomb back to the launch site with all the expensive ground support equipment around.
Neutron is designed to be reusable with a turnaround time of just 24 hours. Rocket Lab does not anticipate needing this capability, but they baked it into the design just because. CEO Peter Beck says that this design principle is responsible for saving so much cost on Neutron because it simplified the recovery and re-launch process dramatically.
Neutron’s second stage is extremely stripped down. Just an engine, a tank, a payload, and some avionics. This means that Neutron will have to undergo stage separation a little higher up than a Falcon 9, due to the lack of aerodynamic protection on the second stage. But it immensely simplifies the second stage design and cuts a ton of costs. The second stage, being so stripped back, does not need a structure to support itself in mounting to the first stage. Instead, the second stage is hanging within the first stage and its fairing, under tension. This design has been field tested before, on ULA Vulcan’s Centaur upper stage, with great results. Worth noting though, that the Centaur upper stage is stainless steel - Neutron’s will be carbon composite, so it will be the lightest second stage ever flown for a comparable size class rocket. So light, that one of the key issues they’ve had to work through with its design is that its engine is almost too powerful for how light the vehicle is. Literally, Neutron’s second stage tank weighs about as much as a Harley Davidson motorbike, and that upper stage engine produces ~600,000 horsepower.
Designed to carry 1500 kg to Mars or Venus.
Archimedes Engine Design:
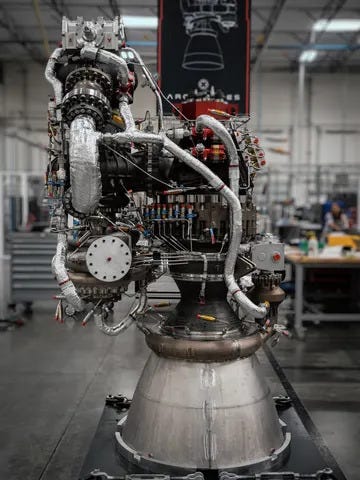
Archimedes is an oxidizer-rich closed cycle engine burning Methalox (methane and liquid oxygen), providing 700-900 kN of thrust at 329s of sea level ISP, not bad efficiency on such a simple engine.
In English, Archimedes is a fine engine, perfect for the job it needs to do. Not too complex, not too expensive, not too tricky to build. It will operate well within its capabilities with low performance loads (chamber pressure), subjecting the engines to less stress over time and granting longer lifespan. The fuel mix is efficient and burns quite clean compared to a fuel-rich cycle, which leaves a lot of soot behind in the engine valves after a firing, making the reuse process significantly trickier. A sea level ISP of 320 seconds is great, cleanly beating the Falcon 9 Merlin engine’s 282 seconds. These engines are designed with a max lifespan of 20 flights, with cheap and reliable reusability at the forefront of their design.
Can throttle down to 50% of max thrust for landing/return to launch site burns.
Approximately 90% of the mass of an Archimedes engine is 3D-printed, using some of the largest additive-manufacturing 3D printers in the world.
Falcon 9 can carry 22,800kg to LEO expendable, 17,400kg reusable. Neutron is aiming for 13,000kg for a barge landing, 8000kg for RTLS (return-to-launch-site), and maybe 15,000kg fully expendable. You might be worried about that minor payload capacity difference, but it’s important to consider that many of today’s satellites are no bigger than shoeboxes. CEO Peter Beck often mentions that Falcon 9’s full payload capacity only appeals to around 3% of the launch market, because the vast majority of individual payloads are not nearly that heavy.
Here is a helpful size comparison between Electron, Neutron, and Falcon 9 (credit to @ NoLifeJordan69 on twitter):
You might notice Sir Peter Beck is highlighted in yellow next to Neutron, for scale.
Spacecraft Family
Rocket Lab has been in the satellite business since their second ever Electron launch, which carried an early Photon satellite demonstration. Since then, Photon has become something of an industry standard satellite platform (also called a bus), flying numerous missions for NASA, the manufacturing mission for Varda, and many others. The Photon spacecraft platform has been adapted into 4 distinct satellites with differing capabilities:
Explorer - Interplanetary Spacecraft Bus
high delta-V spacecraft capable of missions to the Moon, Mars, Venus, as well as highly eccentric Earth orbits, geosync orbit, and Earth-Moon and Earth-Sun Lagrange points.
deep-space capable radiation protection, avionics systems, and ranging transponders.
gained flight heritage for NASA’s Capstone mission and will take ESCAPADE spacecraft to Mars.
Can be launched from Electron and other small launch vehicles
Lightning - Long Lasting Missions Platform
designed for long lasting, high power missions in LEO carrying communications or remote sensing/imagine payloads.
This satellite platform is derived from Rocket Lab’s SDA Globalstar and MDA tranche 2 constellations.
Designed for 12+ year orbital lifespan, incorporating redundancy into multiple critical systems.
Can be launched from Neutron or other medium launch vehicles.
Pioneer - Dynamic Space Operations Bus
This bus is derived from Rocket Lab’s Photon spacecraft for Varda, and is capable of capsule re-entry as well as numerous other highly configurable mission profiles.
Can be launched from Electron, other small launch vehicles, or medium/heavy launch vehicles.
Photon - Original Satellite Bus
designed from a modified Electron kick stage, with power, propulsion, avionics, and comms integrated.
Designed for launch on Electron and other small launch vehicles.
What makes these spacecraft so special is their propulsion systems. Rocket Lab has developed the 3D-printed Curie and HyperCurie 3rd stage engines, featuring engine re-light capabilities. The re-light capability is what allows these spacecraft buses to perform such complex orbital maneuvers, such as the deployment of two spacecraft to completely separate orbits 500km apart. No other private company has this kind of orbital propulsion technology unless you count SpaceX’s Crew Dragon capsule, which is not a commercial offering.
Space Systems
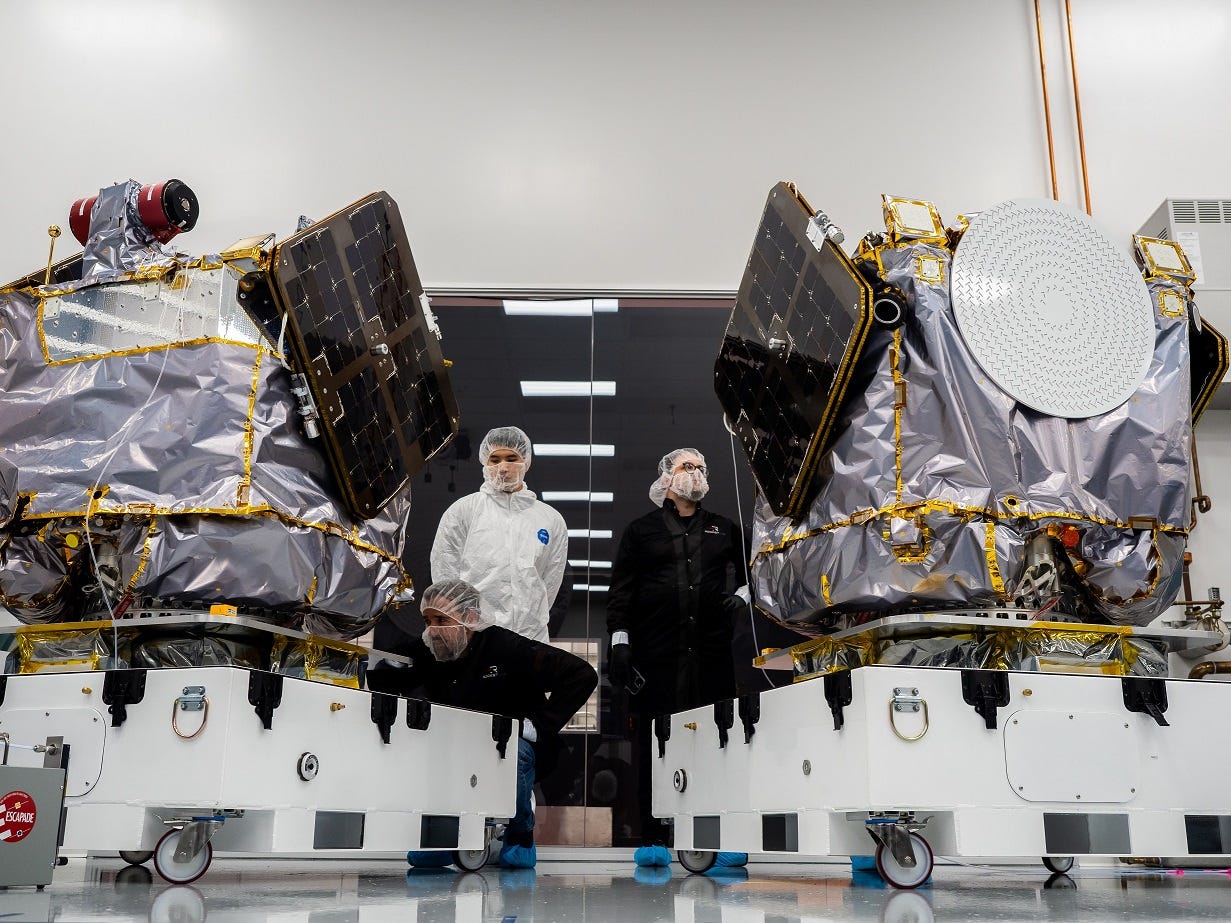
Rocket Lab’s satellite components have flown on over 1,700 missions and in 2023, 38% of everything launched into space globally had a Rocket Lab logo on it. Let’s talk about how they accomplished that:
Through vertical integration, Rocket Lab manufactures all the following spacecraft components in-house.
Star trackers: used for attitude and orientation control, star trackers are designed to measure a satellite’s orientation with respect to subject stars. This is how spacecraft know what direction they’re pointing on orbit.
Reaction wheels: small frictionless and vacuum rated wheels that can spin in a variety of speeds and directions, allowing spacecraft to very precisely control their orientation on orbit. These wheels abuse a little trick called the conservation of angular momentum to make spacecraft rotate - the wheels spin one way, the spacecraft must spin the other.
Payload separators: these separate payloads from launch vehicles. Rocket Lab’s separators have a 100% success rate, so they make this look easy, but these are complex systems and can ruin a whole mission if they fail.
Satellite dispensers: These boxy rectangular structures open up and push many small satellites into orbit very efficiently.
Space grade solar systems: Rocket Lab is one of two US based suppliers of space grade solar systems, from individual cells to large panels and assemblies. Rocket Lab’s panels boast the highest efficiency on the market at 33%.
Radios: Rocket Lab’s Frontier series of radios can provide telemetry, tracking, and control through S and X-bands.
Satellite buses: Buses are the central body of spacecraft, providing power, comms, positioning, propulsion, and more critical functions. Essentially, a spacecraft bus is a complete satellite without a payload (payloads can be optics for Earth imaging, communications technology, or customer specific payload capsules like Varda’s manufacturing capsules).
Spacecraft and ground control software: Though invisible, software plays an extremely critical role in spacecraft and ground control operations, including automatically handling launch processes and ground support equipment processes to support launch.
Composite structures and COPV: Rocket Lab got so good at making composite structures for Electron cheaply and efficiently, that they turned their composites expertise into a separate line of business, selling specialized structures like carbon overwrapped pressure vessels (COPV), which are carbon fiber-wrapped fuel containers with contents under very high pressure.
All these products allow Rocket Lab to be the first truly end-to-end space company. They make and sell nearly everything a customer needs to build a complete satellite, with much lower cost, shorter lead times, and higher production than many traditional satellite components manufacturers.
Space Services
“We are going to launch so much fucking shit into low Earth orbit.”
Space Systems and Launch are pretty obvious. You’ve got to build the satellites, then put them in orbit. But what about Space Services - what can these satellites do up there?
The answer is, of course, form constellations - large networks of satellites in LEO that can serve a variety of purposes, from communication, to Earth imaging, to orbital factories. I think the opportunity here is best summed up with an excerpt from Ashlee Vance’s book, When the Heavens went on Sale - I’d highly recommend it, it was a huge help with writing this article.
“The future that all these space buffs have already started building is one in which many rockets blast off every day. Those rockets will be carrying thousands of satellites that will be placed not all that far above our heads. The satellites will change the way communications work on Earth by, for one, making the internet an inescapable presence with all the good and bad that entails. The satellites will also watch and analyze the earth in previously unfathomable ways. The data centers that have reshaped life on our planet will be transported into orbit. We are, in effect, building a computing shell around the planet.”
We are already seeing a massive increase in satellite launches to LEO for a variety of end goals: constellations, earth imaging, orbital factories, exploration, and government projects.
Historically, internet and GPS services have been provided by “a handful of exquisite birds” in higher orbits like MEO (medium Earth orbit) or geosynchronous and geostationary orbit, unique orbits where a satellite’s orbital period matches the Earth’s rotation such that the satellite stays above the same spot on Earth as it orbits. Sounds super handy for 24/7 coverage, right? Problem is, to get an orbital period that slow, your satellite needs to be around 35,000km up - space begins at just 100km up, a threshold called the Karman Line, and LEO peaks out at around 2000km. The further you are from Earth, the higher the interstellar and solar radiation you must contend with.
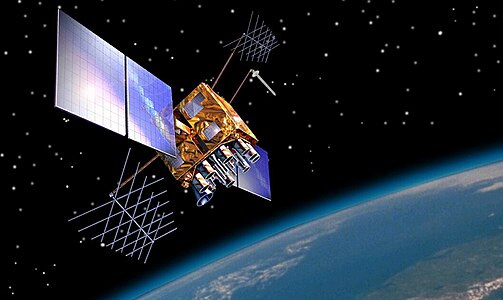
Satellites in geosync orbit are subjected to the worst of the outer Van Allen Belt, a belt of heightened electromagnetic activity from 13,000-60,000km. Essentially, passing through the Van Allen Belts is like passing through a live battle between Earth’s magnetic field and the solar wind, and your spacecraft will be subjected to all the radiation that comes with that. Everything that orbits up there must contend with these belts, so these spacecraft needed to be bulkier and more radiation resistant, making them up to 6x heavier than something like a Starlink sat.
Not to mention, the amount of Delta-V (measure of a rocket’s ability to change its velocity, measured in meters/second) you need to reach that orbital height begets the need for a lot of fuel and a big rocket - a 6x payload increase from a typical LEO sat demands a rocket orders of magnitude larger. Without getting into the rocket equation here, this meme sums the problem up pretty well:
These disadvantages of geosync orbit have led to numerous companies to pursue a different approach. Instead of sending one bulky, billion dollar satellite so high up, they decided instead to place constellations of many smaller, cheaper satellites in much lower orbits, LEO being the most popular destination. Many more satellites can be launched at a time this way, which allows for more total processing power, and you can get 24/7 global coverage with a large enough constellation - not to mention, the time it takes signal to reach satellites in LEO is a noticeable amount faster than the time taken to reach a geosync satellite, around 500 milliseconds faster. If you’ve ever played an online game, you know how significant that extra half second is.
Companies like SpaceX’s Starlink, Amazon’s Project Kuiper, OneWeb, and AST SpaceMobile are great examples of communications and internet providing constellations operating in and around LEO. Companies like Synspective and Capella Space do Earth Imaging, and so far, Varda is the only company to date that has achieved orbital manufacturing. There have also been a few IoT satellites making their way to orbit recently, which is pretty neat to see!
The biggest and brightest constellation deployed to date is from Starlink, which is estimated to bring in >$6bn in revenue from ~3 million subscribers and put up its first FCF breakeven year in 2024 (Quilty Space), to give you an idea of the scale here. They have between 4,000-6,000 operational satellites currently on orbit, with plans to launch as many as 40,000.
Let’s break down the economics of these constellations just a bit here. The average satellite in LEO can last 7-10 years depending on a few factors - orbital height, surface area, and fuel load being the most important. The internet or imaging services these satellites provide will generate high margin, recurring revenue after you get past the associated launch costs.
It’s not easy to get visibility into the deeper economics of constellations - AST SpaceMobile is publicly traded but AFAIK they haven’t got their constellation fully deployed - I think Starlink is the best available information source currently.
Internal Starlink documents project that at 30bn in revenues they’d make 60% operating margins. Payload estimates that SpaceX will pull in $13.3bn in topline this year, $6.8bn from Starlink.
An estimated 10,000 satellites need to be launched by 2030, excluding Starlink and Chinese launches, and Rocket Lab is very well positioned to not only manufacture many of these satellites, but to launch them as well, even before they get to work on their own constellation.
Rocket Lab has been saying they want a hand in Space Services since 2020, but it has become a little more central to their messaging as time goes on.
CEO Peter Beck likes to say that companies who own “the keys to space” (a rocket) and the tools used for orbital operations (spacecraft) will be much better positioned to monetize space assets than others. If you can make your own constellation from scratch and launch it too, your costs will be significantly lower, thus you’ll have higher gross margins. SpaceX has mostly pulled this off on launch but I would bet they don’t make all their satellite components in house. Their exact manufacturing data is classified so we’ll probably never know.
CFO Adam Spice has stated that Rocket Lab plans to use proceeds from their recent convertible offering to acquire some kind of payload capability, whether it be SAR imaging, optics, communications, or ideally all 3 capabilities.
Rocket Lab’s Global Facilities:
Launch Complex 1 (LC-1) - Mahia Peninsula, NZ

First ever privately owned launch site, constructed on New Zealand’s Mahia Peninsula in 2015. This pad makes Rocket Lab the only launch provider with a pad in both hemispheres.
FAA-licensed spaceport, where Rocket Lab is licensed to launch every 72 hours for the next 26 years - 120 launch slots/year, a far higher cadence than US public launchpads allow for, given competition between domestic launch providers and intense regulatory scrutiny. This 120/year figure is greater than all current annual launches from US spaceports combined.
Can service orbital inclinations from sun-synchronous orbit (near polar) to 30 degrees inclination, which captures the majority of satellites launched to LEO.
Features two launchpads for redundancy and increased launch cadence capability.
The launch site and all supporting infrastructure were built entirely by Rocket Lab, with no help from contractors and no government funding - making it the only privately owned and operated spaceport today built without government funding.
Rocket Lab controls everything at this facility, the operations, the budget, the schedule, rocket prep and payload integrations, the tracking and range finding, mission control, everything - they can move whatever they want whenever they want here, which allows them an unprecedented level of control over launch operations, extremely helpful when servicing customers with specific mission requirements on very fast timelines.
Not to mention, typical launch fees at government owned launch sites, say a NASA spaceport, can range in excess of $1mm - around 1/5 of Electron’s entire cost.
This site is an extremely important strategic asset for Rocket Lab. Located on New Zealand’s remote Mahia Peninsula, the location of this launch site is likely its most strategic component. For every rocket launch out of the US, the FAA and a whole host of airlines and marine operators must coordinate a ~2000 sq. km closure of airspace and/or marine shipping space within a certain radius of the launch site. This process is complicated and costly for airlines, marine operators, and launch providers alike, and is largely responsible for the difficulties in estimating launch timing and authorization approval when launching from the US. I’ve seen US launches scrubbed because of stray watercraft or airplanes entering the exclusion zone accidentally - it’s rare but it can and does occur. Airlines hate this process as well, as it can lead to flight delays and substantial revenue losses. NZ is the perfect spot for a launch site, because it lacks this troublesome baggage. As CEO Peter Beck said in a 2019 Ted Talk, the ideal spot for a high-frequency launch site is, “a small island nation in the middle of nowhere, with no neighbors, and no air traffic.” Better yet if you can find a remote, sparsely inhabited peninsula sticking off such an island.
Featuring two launchpads for redundancy purposes, this launch site and all its supporting infrastructure were built without ANY external contractors or government support whatsoever, and it remains the only spaceport located in NZ. In fact, in order to launch from this site in the first place, Rocket Lab had to coordinate the signing of a bi-lateral treaty between the governments of the US and NZ. NZ did not even have a regulatory body to govern aerospace activity before Rocket Lab, so the NZ government had to create a space agency and a whole bunch of new rules and regulations for the space industry Beck essentially gifted them on a silver platter. Fun note here, they literally knighted him for this in June. His official title is Sir Peter Beck now.
The land that LC1 is built on is owned by the Māori people, early Polynesian settlers of NZ that arrived on boats in the early 1300s. In a 2023 census, the Māori people represented just under 20% of New Zealanders. Peter Beck in several interviews described the process of negotiating with the Māori for their land use, saying that he met the Māori leaders in a donut shop of all places. When asked about the use of their land for rocket launches, the Māori leaders said something to the effect of “Well, we have been trying to diversify our land use streams away from cattle and beef, so this looks pretty promising.” Beck really did the work for this himself, at one point singing a Māori welcome song in their language, by himself, to an entire group of Māori. He says his singing was so bad, that the Māori elders had to sing along with him to make him feel a little bit better about it.
And Rocket Lab, in difference to SpaceX at Boca Chica, actually cares about the well being of their neighbors, having created scholarship programs for Māori locals and investing in their community wherever they can - they also named their first ever test rocket launch after the Māori word for space. SpaceX, instead, has a notorious reputation of buying up land near their Boca Chica spaceport, calling local landowners obsessively, sending lawyers to their properties constantly, demanding them to sell their homes, not to mention routine beach and marine space closures. Many Boca Chica locals bitterly hate SpaceX for these reasons. Rocket Lab, however, is far too classy for this sort of thing and they retain a very positive relationship with the Māori people and all other stakeholders in their global affairs.
Launch Complex 2 (LC-2) - NASA Wallops, Virginia
Located at NASA’s Wallops spaceport on Wallops Island, Virginia.
Completed in December 2019, this facility was built specifically for the discreet launch of US government payloads from US soil.
Rocket Lab is licensed to launch 12x/year from this facility, bringing their total annual launch slots to 132. This site has pretty low activity, so Rocket Lab has access to a good amount of the launch calendar at the site. But this gives you a better understanding of how critical the NZ launch site is to their operations, being that it has 10x the annual launch allowance of this site.
Rocket Lab has constructed their own mission control and integrations facilities just outside the gate of the Wallops facility, separate from government assets but close enough that they can take advantage of certain ground support infrastructure already in place at Wallops.
Supplements orbital inclinations already serviced by LC1.
Launch Complex 3 (LC-3) - NASA Wallops, Virginia
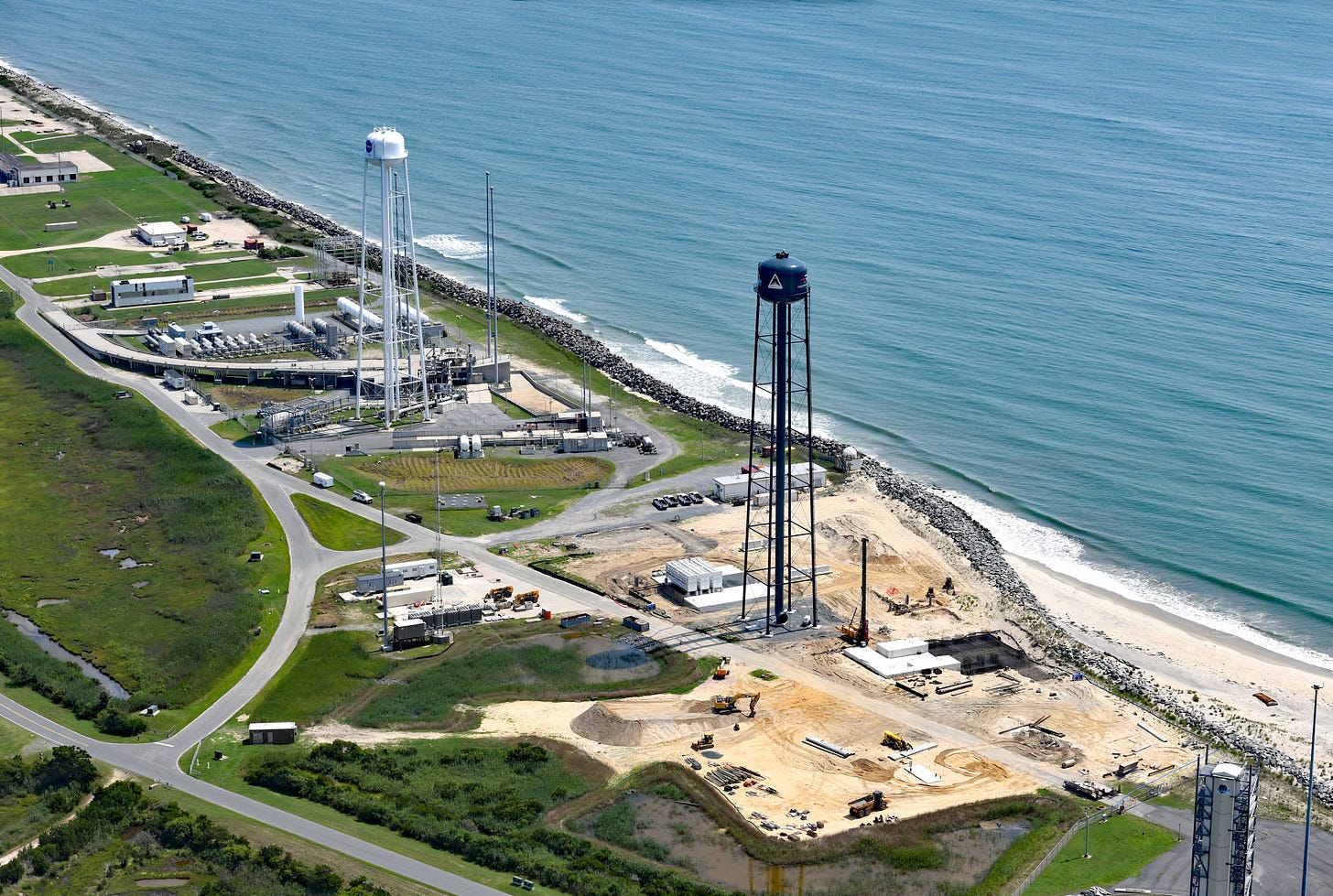
Designated Neutron Launch site, currently under construction at NASA Wallops.
A lot of the R&D and Capex spend associated with rocket development is just “pouring concrete”, as CEO Peter Beck would put it. Once this facility is complete and Neutron prepares for it’s first launch, we will see a significant reduction in Neutron development spend, currently pegged at $40mm per quarter.
US Headquarters - Long Beach, California
Management of sales, business development, and corporate administrative functions occurs here, plus some R&D and remote launch functions.
Engine Development Center - Long Beach, California
Primary propulsion and avionics manufacturing center.
In may 2023, Rocket Lab successfully bid $16.1mm for Virgin Orbit’s former headquarters, as the lease was auctioned off in Virgin’s bankruptcy proceedings. This 144,000+ square foot facility had been recently re-tooled with around $100mm of investment put into it, so Rocket Lab scooped this facility up for a fraction of the cost of building a new facility, at 16 cents on the dollar. This facility also just happened to be two blocks down the road from Rocket Lab’s US headquarters in Long Beach. Rocket Lab now uses this facility for engine production and development, both for Rutherford and Archimedes engines. I think most would agree, it’s pretty metal to turn your former competitor’s HQ into a rocket engine factory after outcompeting them through to their bankruptcy. Another interesting tidbit here: Around a decade ago, when CEO Peter Beck went out to raise a second round of VC funding for his company, the question he was asked most frequently was, “How are you going to compete with Virgin?” Silicon Valley VCs never saw Rocket Lab to have a favorable match up against Virgin in the future - Virgin had initially raised $1.2bn, $1.1bn more than Rocket Lab’s first raise, and Virgin was backed by billionaire Richard Branson. But just look at them today! Virgin is on death’s door and Rocket Lab is scooping up their assets for pennies on the dollar, as the Aussies would say, you truly love to see it.
Auckland Complex - Auckland, NZ
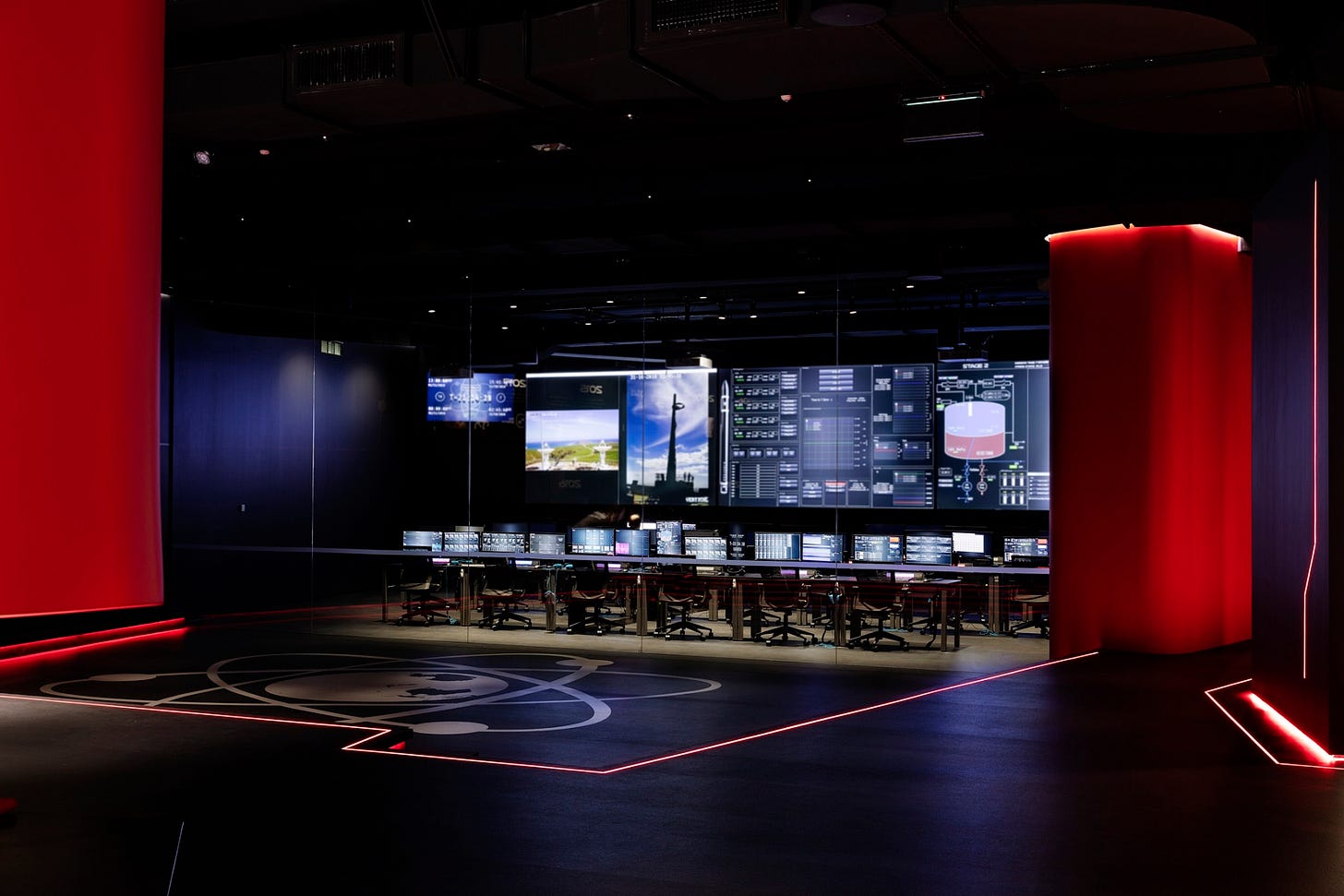
Complex of four adjacent leased buildings housing Rocket Lab’s NZ mission control center and NZ headquarters, R&D and testing facilities, Electron composites, batteries, and Photon kick stage production lines, and Electron integration facilities.
Can produce around 2000 reaction wheels/year - they had to commit to doubling the old production rate due to a large mega-constellation customer that many people believe is Amazon’s Project Kuiper, requiring as many as two to three thousand reaction wheels per year.
This facility has some really neat design choices going for it - I won’t mention all of them here, but the entrance is designed with a lot of inspiration taken from 2001: A Space Odyssey, CEO Peter Beck’s favorite space movie, and it looks really neat.
Archimedes Test Complex - NASA Stennis, Mississippi
Utilizes existing A-3 test stand for primary engine testing
Will be used for Archimedes engine testing and development
NASA Stennis has a rich history as an engine testing site, as it played a crucial role in development of the Saturn V’s F1 engine.
Composite Structures Complex - Warkworth, NZ
This 70,000 square foot facility was the home of SailGP, producers of carbon composite catamarans for the SailGP racing league, before the company decided to relocate to the UK in October 2023. NZ has a rich history in high quality carbon composites, mostly due to the pursuit of ever-faster racing boats like SailGP’s.
Rocket Lab was already contracting SailGP for carbon composite Electron components, so they decided to take over their facility as SailGP left, retaining over 90% of site employees and the facility’s cutting-edge manufacturing equipment, including “an autoclave, ovens, composite material cutting plotters, CNC metal machining equipment, and large-scale CNC composite machining equipment to support accelerated R&D and production.” (I’d hyperlink this here, but the page isn’t showing - Google “SailGP Rocket Lab.”)
Rocket Lab is now planning to use this facility to continue Electron component production and to fast track development and construction of Neutron’s large composite structures. A win for NZ, where high quality composites have had a home for decades thanks to SailGP. Every NZ news source I’ve looked at seems quite happy that these skilled manufacturing employees are staying in NZ.
Space Structures Complex - Middle River, Maryland
In November 2023, Rocket Lab announced plans to establish a new manufacturing center in Middle River, Maryland, to supplement their carbon composites and satellite components manufacturing capabilities.
This 113,000 square foot facility was formerly Lockheed Martin’s Vertical Launch Building, used by Lockheed’s predecessor company since 1929. Lockheed announced plans to leave the site in early 2021 - they had been using it primarily for launch systems for Navy warships (Baltimore AP).
Rocket Lab will now use this site to manufacture carbon composite spacecraft buses, structural assemblies, solar panel components, satellite dispensers, heat shields, COPV, launch vehicle structures, and more.
This factory features the automated fiber placement machinery that will build Neutron’s large composite structures, including the largest automated fiber placement machine of it’s kind in the world:
Via: Rocket Lab I could write another 14,000 word article on Rocket Lab’s absurdly advanced rocket manufacturing techniques alone, but they did publish a really cool YouTube video on this specific fiber placement machine that I would definitely recommend watching.
This factory is located right on the water. Flight ready Neutron rockets will board a barge from here, and float down from Baltimore, through the Chesapeake Bay to Wallops Island for launch, a distance of around 164 miles as the crow flies. This is notably lower than the distance that Falcon 9 and competing rockets must travel for launch, providing a small relative boost to Neutron’s overall efficiency.
Facilities Operated Through Acquisition
Since 2020 Rocket Lab has acquired 4 of its key suppliers in an effort to further vertically integrate production of various space systems, including space-grade solar panels, space operations software, reaction wheels, and separation systems. Rocket Lab conducts these acquisitions to shorten component lead times and increase production. As CEO Peter Beck says, “If the component is too annoying to buy, we need to own it.”
SolAero, Space-Grade Solar Cells Supplier - Albuquerque, NM
SolAero is the most interesting of these acquisitions, being a trusted, long-time supplier of space-grade solar panels. Creating these panels (and the chips that power them) is exceptionally tricky due to the high radiation tolerances needed to keep chips from frying in Earth orbit.
SolAero panels are best in class and trusted by a vast array of commercial and government entities. The company’s panels have flown on the James Webb Space Telescope, NASA’s Lucy mission to the Jupiter Trojans, and on NASA’s Mars helicopter Ingenuity.
Currently, there are over 1,100 satellites in orbit that rely on SolAero’s panels, and through SolAero, Rocket Lab now offers the highest efficiency space-grade solar panels on the commercial market, supplying everything from small solar cells for smallsats, to entire solar arrays used on much larger spacecraft.
One key aspect of this acquisition is the supply environment for space-grade solar panels, which has historically been pretty constrained. Rocket Lab is now one of two US based suppliers of this key technology, and through this acquisition, Rocket Lab has committed to expanding production lines for these components to meet rapidly growing demand - taking a $24mm grant from the CHIPS act and $25mm in state incentives to double their production capacity, expanding their New Mexico facility by 25,000 square feet.
Advanced Solutions, Spaceflight and Ground Control Software - Littleton, Colorado
Acquired in October 2021, Advanced Solutions (ASI) is an industry leader in in-flight software, ground infrastructure software, mission simulations, and spacecraft guidance, navigation, and control programs. Their MAX software suite has a racked up a cumulative 234 years in space and is designed to be an off the shelf, commercialized solution to fit this niche. Though invisible, software is an extremely crucial component to any mission. I’ve seen plenty of missions go awry due to software issues, and it’s tragic every time. ASI’s long track record of providing capable and mission proven software is a great addition to Rocket Lab’s Space Systems portfolio.
Planetary Systems Corporation - Silver Spring, Maryland
Acquired in 2021, PSC has been a key supplier of spacecraft separation systems for over 20 years, with a perfect 100% product reliability rate. These guys make traditional payload separators in the form of their Lightband series, as well as satellite dispensers. These Lightband separators have flown on Atlas V, Antares, and are heavily favored for Falcon 9 rideshare missions and Starlink payloads alike - they’re 1/3 the weight and 1/2 the height of typical clamp separators, with the lowest payload integration time in the industry. Their satellite dispensers have also deployed more than 60 satellites over 11 years.
Sinclair Interplanetary - Toronto, Canada
Acquired in 2020, Sinclair Interplanetary is a leading manufacturer of star trackers and reaction wheels. Currently, they have over 240 reaction wheels on orbit performing well, and they recently signed a deal to provide 2000-3000 reaction wheels per year to an unnamed large megaconstellation customer that many believe to be Amazon’s Project Kuiper. In order to meet demand for this, Rocket Lab put in a new production facility in Auckland capable of producing 2000 reaction wheels per year to meet demand from constellation customers. Sinclair also has over 140 star trackers on orbit right now.
I’d like to mention here, all of Rocket Lab’s facilities are clean, like you could eat off the floor clean. All tools organized and put in their right places, no stray components, no messes or spills, with spotless, shining floors.
Leadership & Governance
Executive Suite:
CEO: Sir Peter Beck
Sir Peter Beck grew up in a red brick house in a small coastal town called Invercargill, on New Zealand’s south island. Peter has said in interviews that one of his first ever memories is of his dad showing him the stars one night and telling him that just maybe, on a planet orbiting one of those stars, is someone looking back at him. Peter credits this moment with his lifelong passion for space travel.
Beck was always an engineer by heart - his childhood home featured a large workshop that he and his two older brothers would spend their nights in, fixing up old junk cars. Beck has no college degree, instead going into the tool and die making trade (creating precision tools used for manufacturing processes) right out of high school. From there, Peter worked in a government lab studying advanced materials, before founding Rocket Lab in 2006.
Peter Beck was so passionate about space travel, he spent his nights and weekends all through his teenage and early adult years developing makeshift rockets. Without any proper testing equipment, Beck would strap two rocket engines to either side of a bicycle and ride it himself. Reportedly, he also tried this approach with roller skates and a rocket backpack.

Beck’s lifelong dream was to work for someone like NASA, but as a foreign national with no degree, that might as well have been impossible. So in 2006, Beck paused his career to take a “rocket pilgrimage” to the US. He went and talked to as many companies and organizations as he could, like NASA and Lockheed, but nobody seemed to think his ideas were particularly interesting, most notably his ideas around dedicated small launch. Nobody really thought it could be done profitably, and Beck left the US relatively disappointed - not just because people weren’t listening to his ideas, or wouldn’t even speak to him in the first place, but also because he felt that NASA and other large space organizations had lost their spark, and were rife with inefficiency, program delays, and cost overruns. By the time his plane back to New Zealand landed, Beck had drawn up the logo for a new company, one he decided to call “Rocket Lab.” If nobody was going to make the things he wanted to see, he decided he would have to do it himself.
The Rocket Lab we know today would not be possible without Peter Beck. It’s his company through and through - he’s CEO, Chief Engineer, and Chairman of the Board, and today he owns 10% of Rocket Lab. That may not seem like a lot, but it’s impressive considering the amount of money Rocket Lab needed to raise since its 2006 founding. Peter Beck did not come into this a billionaire, unlike many of his competitors. What he has accomplished with so little blows anything SpaceX has ever done clean out of the water, in my opinion.
CFO: Adam Spice
Adam Spice joined Rocket Lab 6 years ago as employee number ~100. before Rocket Lab, Adam Spice spent 25 years in the semiconductor industry, holding CFO roles at multiple semiconductor and specialized electronics companies. He holds a BBA from Brigham Young and an MBA from UT Austin, a school most known for its contributions to the cutting edge of STEM research, including aerospace.
Chief Engineer - Special Projects: Shaun O’Donnell
Shaun joined Rocket Lab in 2007, leading development of a number of crucial space systems. He has served as head of Rocket Lab’s GNC division and as EVP - Global Operations. He holds an electrical engineering degree from the University of Auckland.
SVP - General Counsel and Corporate Secretary: Arjun Kampani
Arjun joined Rocket Lab from famed Saturn V engine developer Aerojet Rocketdyne, where he served as SVP overseeing corporate law, governance, litigation, M&A, and more. Before Aerojet Rocketdyne, Arjun was the top M&A lawyer at General Dynamics. He holds a JD from Case Western Reserve University.
VP - New Zealand Operations: Alek Derejian
Alek oversees day-to-day operations at Rocket Lab NZ. Before Rocket Lab, he spent 19 years with Rolls Royce’s Aerospace division specializing in engine and turbine manufacturing and testing.
VP - Space Systems: Dr. Brad Clevenger
Dr. Clevenger provides strategic leadership to Rocket Lab’s Space Systems team. Prior to Rocket Lab, he helped lead SolAero from its 1998 start to taking the largest market share in space grade solar products. Before SolAero, he helped develop nuclear reactors for the Navy. His PhD is from UT Austin.
VP - Neutron: Shaun D’Mello
D’Mello leads development of the Neutron Launch vehicle and associated ground systems. He also oversaw Electron development, so a lot of Rocket Lab’s prestige could probably be credited to this guy. He holds a degree in Aerospace Engineering from the University of Sydney.
VP - Global Launch Services: Brian Rogers
Mr. Rogers is responsible for Rocket Lab’s global defense and civil launch portfolios. Previously, he was Advanced Systems Manager at Ball Aerospace and helped develop ULA’s Vulcan Centaur, Atlas V, and Delta IV.
VP - Government Operations and Business Strategy: Andrew Bunker
Responsible for the execution of Rocket Lab’s federal, state, and local government strategy. He brings more than a decade of experience in legislative affairs and space regulation. Prior to joining Rocket Lab in 2021, Bunker was Director of Government operations at ULA.
Board of Directors:
Sir Peter Beck - Founder, CEO, and Chairman of the BOD
Lt. Gen. Nina Armagno - Independent Director
Lt. Gen. Armango joined Rocket Lab’s BOD in 2023 after more than 35 years serving in leadership positions in the US Air Force and Space Force.
Dr. Edward Frank - Independent Director
Joining Rocket Lab’s BOD in 2022, Dr. Frank bring over 35 years in technical systems leadership experience, including serving as VP of Macintosh Hardware Systems Engineering at Apple.
Dr. Michael Griffin - Independent Director
Dr. Griffin is the founder of LogiQ Inc, a consulting business serving aerospace and national security customers. Previously, he spent two years with the Pentagon as Under Secretary of Defense Research and Engineering, overseeing all US Defense department research and development.
Matt Ocko - VC Investor
John A. Olson - Independent Director
Brings over 40 years of experience in the semiconductor industry, having served at Intel for over 20 years.
Merline Saintil - Independent Director
Brings over 20 years of leadership experience in the technology and business sector, including having played key roles in the development of Intuit, Yahoo, PayPal, Adobe, and Sun Microsystems.
Alex Slusky - VC Investor
Kenneth Possenriede - Independent Director
Joining Rocket Lab’s board on 8/22 (made the stock pop 5%), Kenneth served as CFO at Lockheed Martin and brings deep expertise in capital markets, as well as industry connections and business scaling expertise.
Conclusion
This article is too long already for me to just repeat the claims I made in the thesis as some sort of conclusion. Instead, in closing, I will say I would recommend Rocket Lab to the risk-tolerant, forward looking investor, and I sincerely hope you will consider an investment in this company based on my article, or that this article can work to re-affirm your previously held convictions about Rocket Lab if you already own shares. Rocket Lab has already done amazing things and is poised to continue operating at the cutting edge of aerospace and defense operations, and it is my personal belief that they will be hugely successful in their future aspirations.
If you enjoy deep dive articles like this one, I also have a series of articles on Samsara Technologies (IOT), an innovative data company using IoT technology to transform physical operations like manufacturing and logistics.
If you feel this article provided value to you, please consider subscribing: for now, it’s free. At some point I will begin monetizing these articles, as this took countless hours of work and a lot of late nights, and I feel this article can provide a lot of value strictly due to the depth of my research and the expanse of coverage here. Also, your boy is a college student and needs to find some way to pay rent without selling off my stock portfolio. If Substack allows it, I will reward my first 100 subscribers with free membership for life, and any subscribers past that will be paywalled for certain articles. Anyways, thank you all for reading this article (especially those actually reading this part), and I look forward to publishing many more articles like this in the months and years to come!
Update 8/29:
Corrected various inaccuracies around Neutron’s current design
Updated Archimedes engine ISP, combustion cycle, manufacturing, and throttling capabilities
Corrected MDA’s acronym
Update 8/31:
Added various images for the extra pizazz and edited some of CEO Peter Beck’s section in Governance & Leadership
Wow, that’s really surprising! I’m amazed at how similar our thoughts are. I also write various posts related to Rocket Lab on my personal blog. By the way, I’m Korean, and all of my blog posts are written in Korean. If you want, I can attach my blog posts for you. You and I think so much alike.Your analysis really moved me. In fact, there has been a lack of accurate analysis on Rocket Lab until now. I also believe that Rocket Lab is the only company that closely follows SpaceX. Especially, both SpaceX and Rocket Lab are wisely solving the dilemmas that launch vehicle companies face. It’s no coincidence that Rocket Lab secured technology in the space systems sector in time for the development of Neutron. It was a thoroughly calculated move. Rocket Lab realized early on that most of the value SpaceX creates comes from Starlink. If you ever need resources from my blog, feel free to contact me personally. I’ll leave my email address and blog link. Please understand even if my English isn't perfect.
email : yh17601@naver.com
blog: https://blog.naver.com/yh17601/223561762319
I'll be waiting for more in-depth analysis.
I've been a Rocket Lab enthusiast for a few months now, but this was a great read. Thanks and you have got a new subscriber.